My 1988 B2200 developed a bad AC clutch bearing. A shop would typically just replace the entire compressor, as shops would likely just pull the compressor if they had to replace an AC clutch, so easier for them just to install and warranty an entire compressor. By the way, these compressors are also getting hard to find new.
Anyway, I’m not “most shops”. When I pulled the AC belt and spun the AC pulley, I could hear and feel that the bearing was bad. I had a used/bad compressor which had a fine AC clutch bearing though, so figured to swap the AC clutch parts except for the electrical coil.
Typically, I just engage the compressor with the engine off, and the AC belt on, to loosen the center nut with the 19mm socket, but I wanted to show what one might do if the AC clutch would not engage due to bad coil, oily clutch, etc. So I removed the AC belt; 14mm gear wrench and a 12mm socket on an extension will be your good friends for this.
I got the loaner tool from AutoZone to hold the pulley immobile while one loosens the nut, but my 19mm socket was too big to fit in the hole.
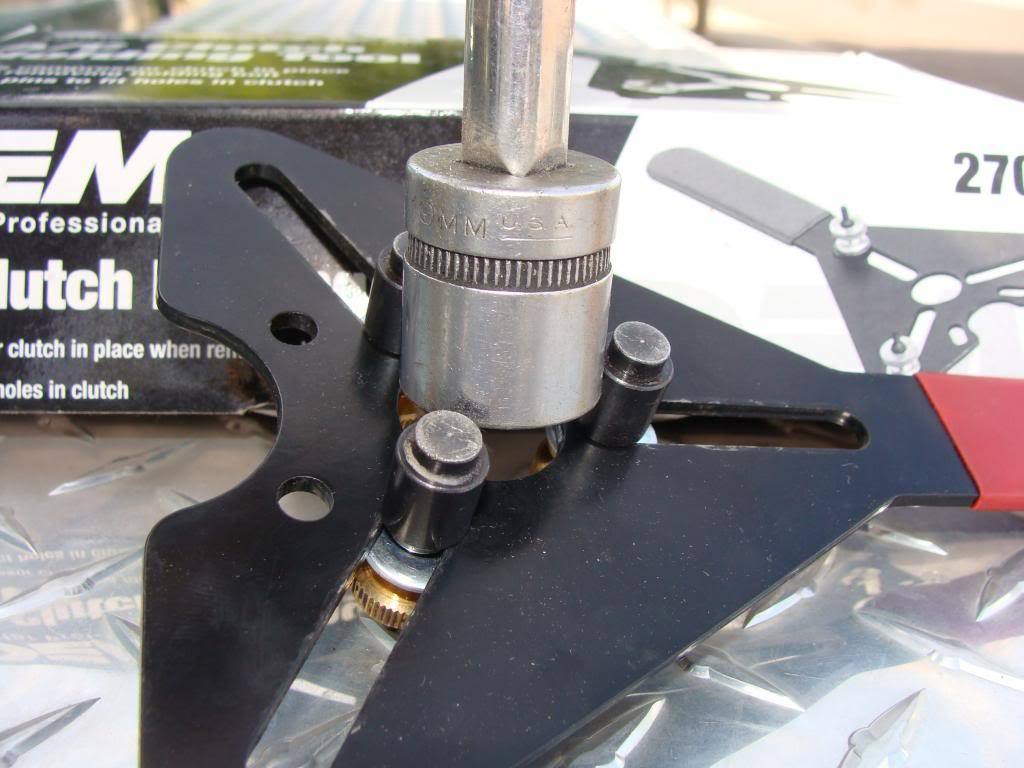
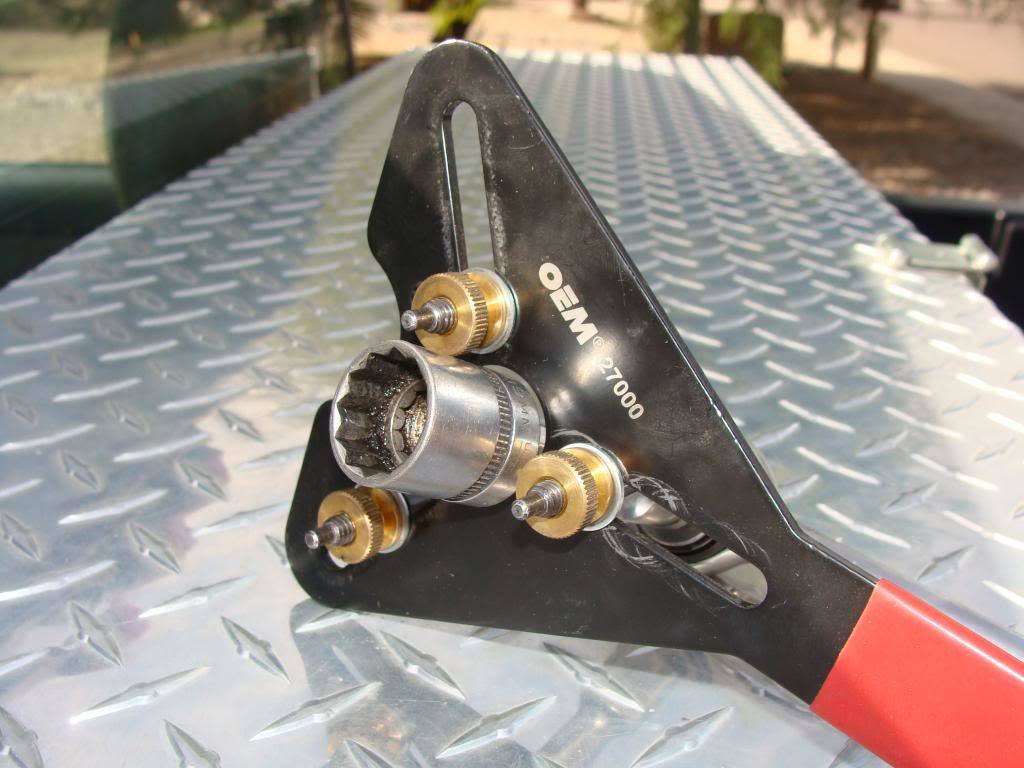
And if I put the socket on the “other side”, then the pegs were too short.
I tried using hex head screws ¼ inch x 20 with the loaner tool but my nut was on too tight.
So I just used a Vise-grips LC1218 pliers to hold the compressor hub steady while I did loosened the center nut.
OK, to pull the hub, a loaner tool didn’t work, so I made my own from these parts:
Three bolts, 2 inches long, thread size ¼ inch x 20 (yes, the holes in the hub are threaded SAE, not metric)
One bolt 2.5 inches long, thread size ½ inch x 13, with matching nut
One washer, 2.0 inch diameter; this will need three holes to be drilled so the three bolts can pass through
One washer with ½ inch hole, 1.25 inches diameter (so the big nut doesn’t come through the hole in the large washer); this will need to be slightly ground in three places. If 2 inch washer has ½ inch hole already, forget this item.
Here’s a mock up of the tool fitting in the hub.
pic
Here’s the tool in use. I threaded in the three ¼ inch bolts into the hub and used the big Vise-grips to hold the nut stationary as I turned the bolt to extract the hub. Some of you who weld might just weld that nut and washer to the bottom of the large washer. I epoxied mine together today after using.
pic
After removing the hub, you’ll need a circlip pliers to remove a circlip, a little tricky, and I used a mirror here to help. The woodruff key for the hub should remain in place. If it comes out, don’t lose it !!!
pic
Then I tapped off the AC clutch using a piece of wood.
pic
Here’s a view of the backside of the AC clutch.
pic
If you want to simply replace the bearing, remove the circlip and tap out the bearing using a big socket (I used a 36mm socket to tap this bearing half out.
pic
Here’s the compressor end showing the magnet coils.
pic
Here, with the better AC clutch simply pushed on.
pic
Then I replaced the big circlip, to hold the clutch in place. Then I added the hub, lining up its slot with the shaft’s woodruff key.
pic
Tighten the center nut while holding the hub immobile like was done for loosening the nut. Replace AC belt, tighten properly. Note that I did NOT have to remove the fan shroud or move it to the side.